Blog Thema
O.E.E. – Optimierung auf einen Blick: Effizienz, Effektivität, Exzellenz
Montagmorgen – 7:30 Uhr. Die Stille der frühen Stunde wird jäh durch das Surren von Maschinen und das geschäftige Treiben in der Produktionshalle unterbrochen. Doch etwas ist anders heute. Die sonst so fließenden Bewegungen der Arbeiter wirken hektisch, die Stirn des Produktionsleiters ist von Sorgenfalten gezeichnet. Der O.E.E. Monitor – die Anzeigetafel für Gesamtanlageneffektivität – blinkt unruhig. Die Effizienz? Unter den Erwartungen. Die Effektivität? Nicht da, wo sie sein sollte. Exzellenz? Heute nur ein Wort in den Unternehmensleitlinien.
Auf der Suche nach dem Warum: Die Entschlüsselung des Produktionsrätsels
Der Grund? Der Kundentakt (KT), die Zeit, die benötigt wird, um ein Produkt herzustellen, das die Kundennachfrage erfüllt, liegt bei straffen 30 Sekunden. Die Zykluszeit (ZZ), die tatsächliche Zeit für die Herstellung eines Produkts, hinkt bei 45 Sekunden hinterher. Eine Lücke von 15 Sekunden, die sich mit jeder Minute, jeder Stunde zu einem wachsenden Berg unausgeführter Aufträge aufsummiert.
Die Frage, die in der Luft hängt, schwer wie die Metallteile, die auf ihre Verarbeitung warten, ist: „Warum?“ Warum schafft es die Fertigung nicht, die Vorgaben zu erfüllen? Sind es die Maschinen, die trotz vorbeugender Instandhaltung den Geist aufgeben? Liegt es an der Organisation, an Prozessen, die mehr Labyrinthe als effiziente Wege darstellen? Oder ist es das Personal, das trotz Anstrengungen und Schulungen nicht mit den Maschinen Schritt halten kann?
Die Lösung liegt in den Daten, die der O.E.E. liefert: Verfügbarkeit, Leistung, Qualität. Jeder dieser Werte ist ein Puzzleteil zur Optimierung des Produktionsprozesses. Verfügbarkeit – Maschinenstillstände reduzieren. Leistung – die Geschwindigkeit der Produktionslinie erhöhen. Qualität – Ausschuss und Nacharbeit minimieren.
Ein Notfallmeeting wird einberufen. Abteilungsleiter, Techniker, das Instandhaltungsteam, alle sind da. Die Stoppuhr tickt. Der Kaffee, längst kalt, wird zur Nebensache. Die Monitore zeigen in Echtzeit, wo die Probleme liegen. Dann schlägt jemand die Integration des Volz-Systems vor, ein intelligentes Instandhaltungs- und Organisationssystem, das verspricht, die O.E.E.-Werte zu revolutionieren. Ein Plan wird entwickelt, Prioritäten gesetzt, Aufgaben verteilt. Instandhaltung hier, Prozessoptimierung da, Schulung dort.
Entdecken Sie mit Volz-System die Kunst der Effizienzsteigerung in Ihrer Produktion. Wir fokussieren uns darauf, die Lücke zwischen Ihrer aktuellen Zykluszeit und dem geforderten Kundentakt zu schließen. Profitieren Sie von der langjährigen Erfahrung unserer Berater:innen und nehmen Sie noch heute unverbindlich Kontakt auf.
Die nächsten Tage werden zur Bewährungsprobe. Jeder Handgriff zählt, jede Sekunde ist kostbar. Langsam, aber sicher, beginnt die Zykluszeit zu sinken. 44 Sekunden. 42 Sekunden. Die Lücke schließt sich. Der Kundentakt rückt in greifbare Nähe.
Es ist ein Rennen gegen die Zeit, gegen Kosten, für Qualität. Aber mit einem klaren Blick auf die O.E.E.-Werte, mit einem Team, das entschlossen ist, die Herausforderung anzunehmen, wird aus dem Montagmorgen ein Wendepunkt. Aus der Krise wird eine Chance zur Verbesserung, zur Effizienz, zur Exzellenz. Denn in der Welt der Produktion ist kein Problem zu groß, kein Fehler zu klein, und keine Optimierung unerreichbar.
ALLE VORTEILE AUF DEN PUNKT GEBRACHT
7 Action points zur Überwindung der aktuellen Krise
Entdecken Sie mit Volz-System die Kunst der Effizienzsteigerung in Ihrer Produktion. Wir fokussieren uns darauf, die Lücke zwischen Ihrer aktuellen Zykluszeit und dem geforderten Kundentakt zu schließen. Mit unserem systematischen Ansatz identifizieren und beheben wir die Gründe für Produktionsverzögerungen – sei es durch Maschinenstillstand, organisatorische Labyrinthe oder Personalentwicklungsbedarf. Unsere Berater:innen, ausgestattet mit langjähriger Erfahrung, stehen bereit, um Ihnen einen maßgeschneiderten Aktionsplan zu liefern. Kontaktieren Sie Volz-System heute noch, um unverbindlich die Weichen für nachhaltigen Erfolg und operative Exzellenz zu stellen.
1. Zieldefinition: z.B. Die Zykluszeit (ZZ) von 45 Sekunden auf den Kundentakt (KT) von 30 Sekunden zu reduzieren.
2. Strategie: Das Volz-System wird eingesetzt, um Echtzeitdaten zu erfassen und eine präzise Analyse der Stillstandszeiten, Produktionsengpässe und Qualitätsmängel zu liefern.
3. Maßnahmen: Installierung von Sensoren und Software des Volz-Systems an allen kritischen Maschinen und Arbeitsplätzen.
4. Schulung des Bedienpersonals und der Instandhaltungsteams im Umgang mit dem Volz-System, um eine schnelle Reaktion auf Anomalien zu gewährleisten.
5. Einrichtung eines zentralen Dashboards, das alle O.E.E.-relevanten Daten visualisiert und in Echtzeit aktualisiert, falls noch nicht vorhanden.
6. Tägliche Review-Meetings, um die so gesammelten Daten zu analysieren und umgehend Korrekturmaßnahmen einzuleiten.
7. Entwickeln eines Belohnungssystems für Teams und Einzelpersonen, die wesentlich zur Verbesserung der O.E.E.-Werte beitragen.
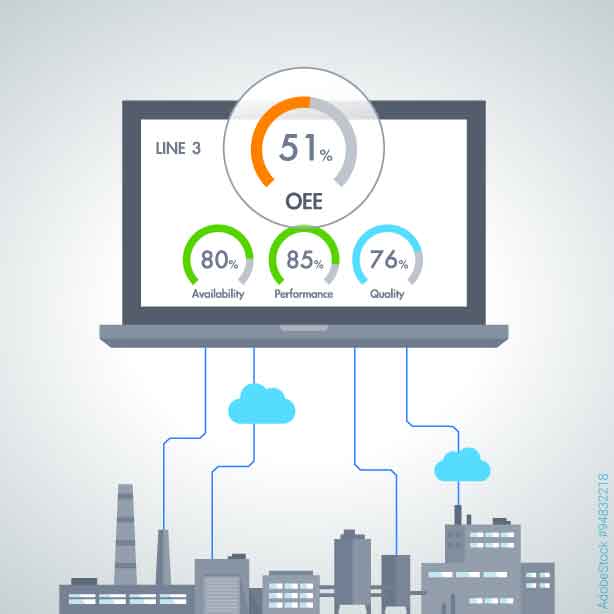
Gerne unterstützt Sie Volz-System bei der Durchführung und konkreten Umsetzung aller notwendigen Schritte, um Ihre Produktionsprozesse durch OEE-Optimierung zu maximieren. Entdecken Sie, wie Sie mit unserer Expertise die Effizienz Ihrer Maschinen und Anlagen steigern können. Nehmen Sie Kontakt mit uns auf!
Die Action Points werden mit Nachdruck umgesetzt. Jeder weiß, dass die Implementierung der Volz-System-Methode der Schlüssel zur Überwindung der aktuellen Krise ist. Mit diesem fortschrittlichen Ansatz kann die Produktionsmenge präzise geplant, Engpässe schnell identifiziert und die Instandhaltung proaktiv gestaltet werden.
Die Hoffnung kehrt zurück in die Gesichter der Anwesenden. Mit dem Volz-System haben sie jetzt nicht nur Daten und Zahlen, sondern einen klaren Fahrplan und die Technologie, die es braucht, um die Produktionsziele nicht nur zu erreichen, sondern zu übertreffen. Der Montagmorgen ist nun nicht mehr nur der Beginn einer Arbeitswoche, sondern der Startschuss für eine neue Ära der Effizienz und Exzellenz in der Produktion.
Häufige Fragen zum Thema Optimierung mit Hilfe von der Kennzahl O.E.E.:
Das Besondere an der Volz-System-Methodik liegt in ihrer außergewöhnlichen Anpassungsfähigkeit und Zugänglichkeit. Diese Methodik erfordert keine spezifischen Voraussetzungen und kann nahtlos in jedes organisch gewachsene Produktionssystem integriert werden. Obwohl vorhandene günstige Bedingungen wie bereits vorhandene brauchbare Daten den Einstieg erleichtern können, ist die Methodik so gestaltet, dass sie auch ohne jegliche Vorabinformationen erfolgreich angewandt werden kann. In solchen Fällen beginnt der Prozess mit der Datenerfassung über ein OEE-Tablet, wobei alle weiteren Schritte entweder parallel dazu oder im Anschluss durchgeführt werden. Diese Flexibilität macht die Volz-System-Methodik zu einem äußerst effektiven Werkzeug für Unternehmen, die ihre Produktionsprozesse optimieren möchten, unabhängig von ihrem aktuellen Stand der Datenvorhaltung.
Bei der Anwendung der OEE-Kennzahl (Overall Equipment Effectiveness) für die Optimierung von Produktionsprozessen gibt es verschiedene Ansätze, die je nach spezifischer Ausgangslage des Unternehmens variieren können. Die Entscheidung, welche Maßnahmen zu ergreifen sind, hängt stark von der individuellen Situation und den vorhandenen Informationen ab. Ein prägnantes Beispiel illustriert diese Herangehensweise:
Angenommen, ein Unternehmen steht vor der Herausforderung, dass es die erforderliche Produktionsmenge nicht erreicht und gleichzeitig über keine Daten verfügt, um die Ursachen hierfür zu analysieren. In einem solchen Fall bietet sich ein niederschwelliger, zugleich effektiver und effizienter Ansatz an: die Datenerfassung über eine OEE-App. Diese App ermöglicht es, Daten manuell in benutzerfreundliche, vorgefertigte Felder einzugeben. Ein solches Vorgehen erlaubt es dem Unternehmen, bereits nach wenigen Wochen erste Aufschlüsse über mögliche Problemfelder zu gewinnen. Die gewonnenen Erkenntnisse können Aufschluss über verschiedene Bereiche geben, beispielsweise über die Ablauforganisation, die Verfügbarkeit von Mitarbeitern und Material, Probleme direkt an den Anlagen oder Maschinen, Ersatzteilwirtschaft oder die Instandhaltungsstrategie.
Diese initialen Daten bilden die Grundlage für weiterführende Analysen und die Ableitung zielgerichteter Maßnahmen. So kann das Unternehmen entscheiden, ob sofortige Verbesserungen möglich sind oder ob umfassendere Schritte geplant werden müssen, die auf einer detaillierteren Datengrundlage basieren. Die Flexibilität, sowohl mit sofort umsetzbaren Maßnahmen zu beginnen als auch fundierte Entscheidungen für langfristige Optimierungen vorzubereiten, macht die OEE-Kennzahl zu einem mächtigen Werkzeug in der Produktionssteuerung und -optimierung.
Wenn die Analyse der OEE-Kennzahl (Overall Equipment Effectiveness) eindeutig auf technische Ursachen für Probleme in der Produktionsgeschwindigkeit und Qualität hinweist, empfehlen wir nachdrücklich, alle verfügbaren Sensordaten der betreffenden Einheit, Maschine oder Anlage zu erfassen. Durch die gleichzeitige Aufzeichnung dieser Sensordaten und Auswertung der OEE-Ereignisse, beispielsweise mithilfe einer spezialisierten OEE-App, ermöglichen wir eine tiefgreifende Analyse. Diese Analyse kann Aufschluss über mögliche Korrelationen zwischen den Sensordaten und den festgestellten Ausfällen oder Qualitätsmängeln geben. Auf dieser Basis können wir Predictive Maintenance – die fortschrittlichste Strategie der Instandhaltung – gezielt einsetzen. Dieser Ansatz ermöglicht es uns, die Anlagenoptimierung hinsichtlich Verfügbarkeit, Qualität, Leistung und Energieeffizienz präzise auf den erforderlichen Kundentakt abzustimmen und somit die Gesamtproduktivität signifikant zu steigern.