Blog Thema
Nicht-bestandsgeführte Lager
Montagmorgen – 7:30 Uhr. Noch nicht einmal der erste Kaffee. Das Management ruft an: Anlagenstillstand. Die Produktionsausfallkosten steigen. Die Ersatzteile werden schnellstmöglich benötigt, damit die Anlage und die Produktion wieder laufen kann. Undurchsichtig organisierte Läger verzögern die Instandhaltung und lassen die Kosten explodieren.
Zum optimalen Stammdatenmanagement Ihrer Ersatzteile
Bei „nicht-bestandsgeführten Lägern“ (Schwarzlägern) handelt sich um Läger, in denen kein Stammdatenmanagement vorhanden ist und die nötige Transparenz der Lager(orte) und des Equipments fehlen. Besonders in der Instandhaltung sind nicht-bestandsgeführte Läger problematisch, da der/die Instandhalter:in die richtigen Ersatzteile zur richtigen Zeit, funktionsbereit und in der richtigen Menge am Reparaturort benötigt. Dies ist nicht möglich, wenn keine Dokumentation bzw. kein Lagersystem über die Lagerorte und der vorhandenen Ersatzteile vorliegt. Im Worst-Case-Szenario kommt es durch nicht auffindbare oder nicht vorhandene Ersatzteile zu verlängerten Produktionsausfallzeiten und den damit verbundenen höheren Produktionsausfallkosten.
Sind die Ersatzteile nicht bestandsgeführt, müssen entweder die Orte abgesucht werden, in denen die Ersatzteile potenziell zu finden sind oder Mitarbeiter:innen ausfindig gemacht werden, welche die Lagerung der Ersatzteile kennen.
Die Uhr tickt und die Kosten steigen.
Oft werden die benötigten Teile als schnelle und kurzfristige Lösung einfach neu bestellt. Diese mehrfache Anschaffung von schon vorhandenen Teilen verschwendet Geld und das nur, weil die Lagerorte und Ersatzteile nicht systematisiert und dokumentiert sind.
Neben den direkten Problemen in der Instandhaltung ergeben sich noch weitere Nachteile:
- Nicht bestandsgeführte Ersatzteile werden in der Regel nicht hinsichtlich ihrer Funktionstüchtigkeit kontrolliert (z.B. Alterungsprozess und Lagerschäden).
- Durch nicht bestandsgeführte Ersatzteile kann die Frequenz der Teile nicht analysiert und die Lagerorte/Lagerbedingungen nicht optimiert werden.
- Datenblätter und Dokumentationen werden meist nicht mitgeführt.
- Die Reklamationen sind komplizierter.
- Es sind keine Zuordnungen zum Equipment vorhanden und ausrangiertes Equipment wird ohne die Ersatzteile entsorgt. Die obsoleten Teile reichern sich an.
- Eine Harmonisierung und Standardisierung sind ohne einen digitalen Zugriff auf die echten Bestellungen fast nicht möglich und die Teile können nicht mit Schlagworten angereichert werden.
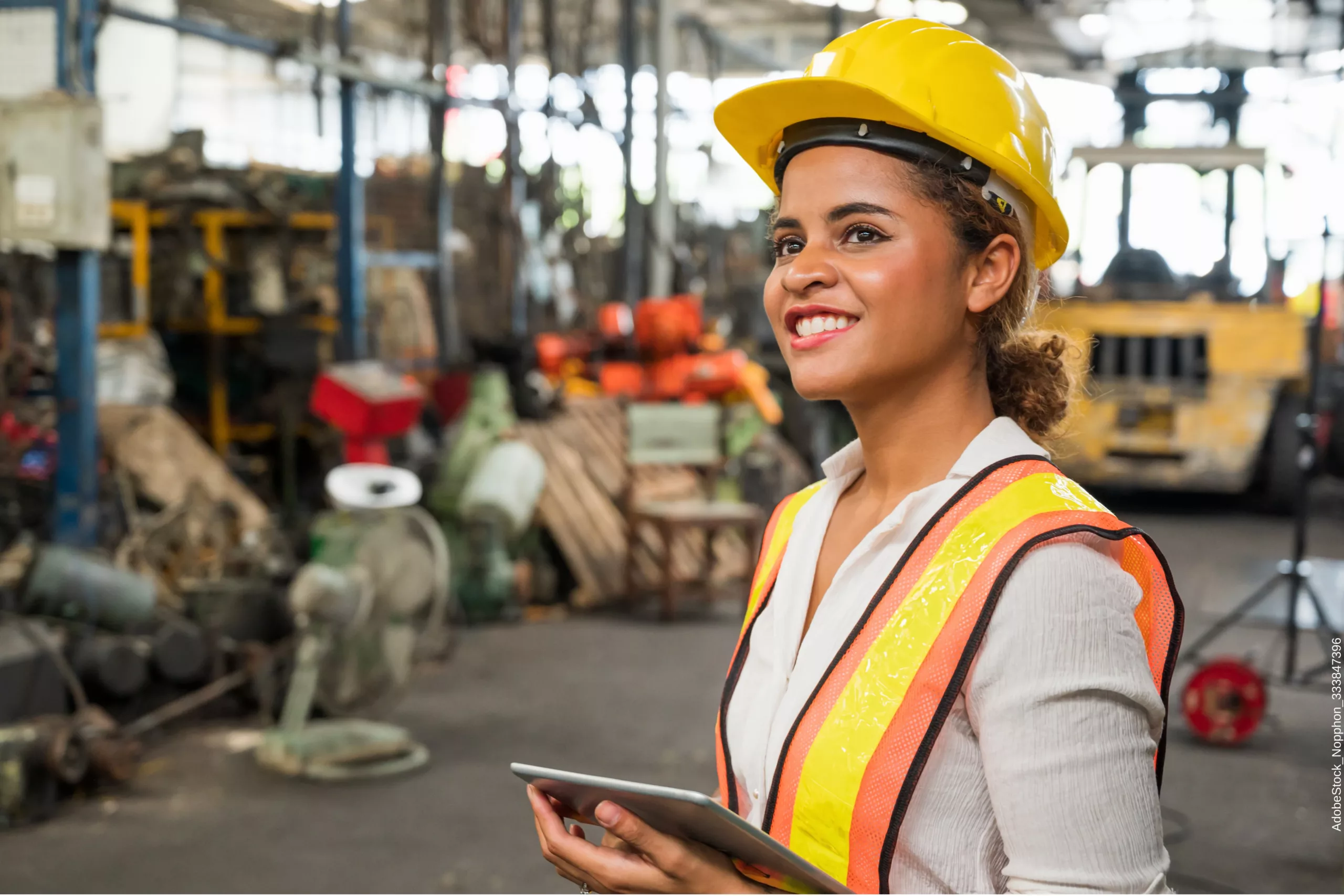
Volz-System berät Sie in der nachhaltigen Strategie und der effizienten Umsetzung eines Ersatzteil- und Stammdatenmanagements für Ihre Anlagen und Maschinen. Profitieren Sie von der langjährigen Erfahrung unserer Berater:innen und nehmen Sie noch heute unverbindlich Kontakt auf.
Durch eine gezielte digitale Aufnahme von Lägern und ein durchdachtes Ersatzteilmanagement können sich erhebliche Kosteneinsparungen ergeben, die sich direkt in den Bilanzen bemerkbar machen. So können die Kapitalbindungskosten durch das Verschrotten obsoleter Teile und der Ermittlung von Dubletten reduziert oder durch die Standardisierungen von Lagerteilen und durch Abschmelzungsprozesse von nicht standardisierten Ersatzteilen Volumeneffekte erzielt werden, um hier nur einige Beispiele für Potenziale zu nennen. Zudem können Lagerteile individuell und leicht zugänglich in ein System eingepflegt werden, was nicht nur einen Überblick verschafft, sondern auch langfristig die Arbeit aller Mitarbeiter:innen erleichtert. Am Ende einer erfolgreichen Digitalisierung stehen alle Lagerteile konsolidiert, in den Attributen harmonisiert, klassifiziert und standardisiert in einem „Vor -IT System“. Dieses Vorsystem ermöglicht eine spätere Migration in jedes andere gewünschte System (z.B. SAP, Maximo). Es geht also nicht nur um eine klare, nachhaltige und organisierte Struktur von Lagerteilen und folglich fundamentalen Kosteneinsparungen an verschiedenen Stellen, sondern auch von einer langfristig optimierten und vereinfachten Datenpflege.
ALLE VORTEILE AUF DEN PUNKT GEBRACHT
6 Schritte zum erfolgreichen Stammdatenmanagement
Der viel bessere Weg als das lästige Versteckspiel mit den Ersatzteilen ist die Nutzung eines gut gefütterten und gepflegten Computerized Maintenance Management System (CMMS), in dem die benötigten Teile schnell gefunden und für die Reparatur reserviert werden können. Bei einem gut eingerichteten EDV-System ist nicht nur die Zuordnung der Ersatzteile zum jeweiligen Equipment oder Anlage (Endverbleib) klar, sondern auch die Stammdaten des Equipments sowie die vorhandenen Mengen und Lagerorte der Teile sind ersichtlich. Falls das Teil nicht auf Lager ist, könnte dieses durch eine relativ einfache BANF (Bedarfsanforderung) bestellt oder Prozesse der Nachbestellung durch ein ausgewähltes Dispositionsverfahren automatisiert werden.
1. Bereinigung von vorhandenen Daten
In einem ersten Schritt sollen eventuell schon vorhandene Daten gesichtet und hinsichtlich ihrer Qualität geprüft werden. Dadurch können mögliche Dubletten erkannt und bereinigt werden. Daraufhin werden die Attribute der Stammdaten harmonisiert. Es wird zudem definiert, welche weiteren technischen Daten benötigt werden. Diese bereinigten und harmonisierten Daten sind die Grundlage zur weiteren Lageraufnahme.
2. Lagervorbereitung
Vor Ort sollte das Lager aufgeräumt werden. Obsolete Teile werden dabei verschrottet oder zumindest gekennzeichnet. Dann werden die aufzunehmenden Teile sortenrein eingelagert und zumindest temporär einem Platz zugeordnet. Auch die Kennzeichnung der Regale erfolgt.
3. Durchführung der Lageraufnahme vor Ort
Die Ersatzteile werden konsolidiert, harmonisiert, klassifiziert und fotografiert sowie mit vorher abgestimmten Merkmalen (vor Ort ersichtlich) angereichert. Eine Vorab-ID (QR- oder Barcode) identifiziert die Teile in einem Datenmanager (zumindest in einer „temporären Aufnahmesoftware“) und der Prozess zur Ein- und Auslagerung wird definiert.
4. Qualitätssicherung der Daten
Die vor Ort aufgenommenen Daten werden nun gegebenenfalls mit Daten aus dem Internet bzw. von den Lieferanten angereichert. Als Option können diese auch aus vorhandenen Dokumentationen gesucht werden. Mithilfe von Algorithmen werden die Bezeichnungen der Ersatzteile harmonisiert. Gleichzeitig kann eine eigene Verschlagwortung mit eigenen Begriffen ergänzt werden. Über die Klassifizierung können die Ergebnisse in 16 Sprachen dargestellt werden.
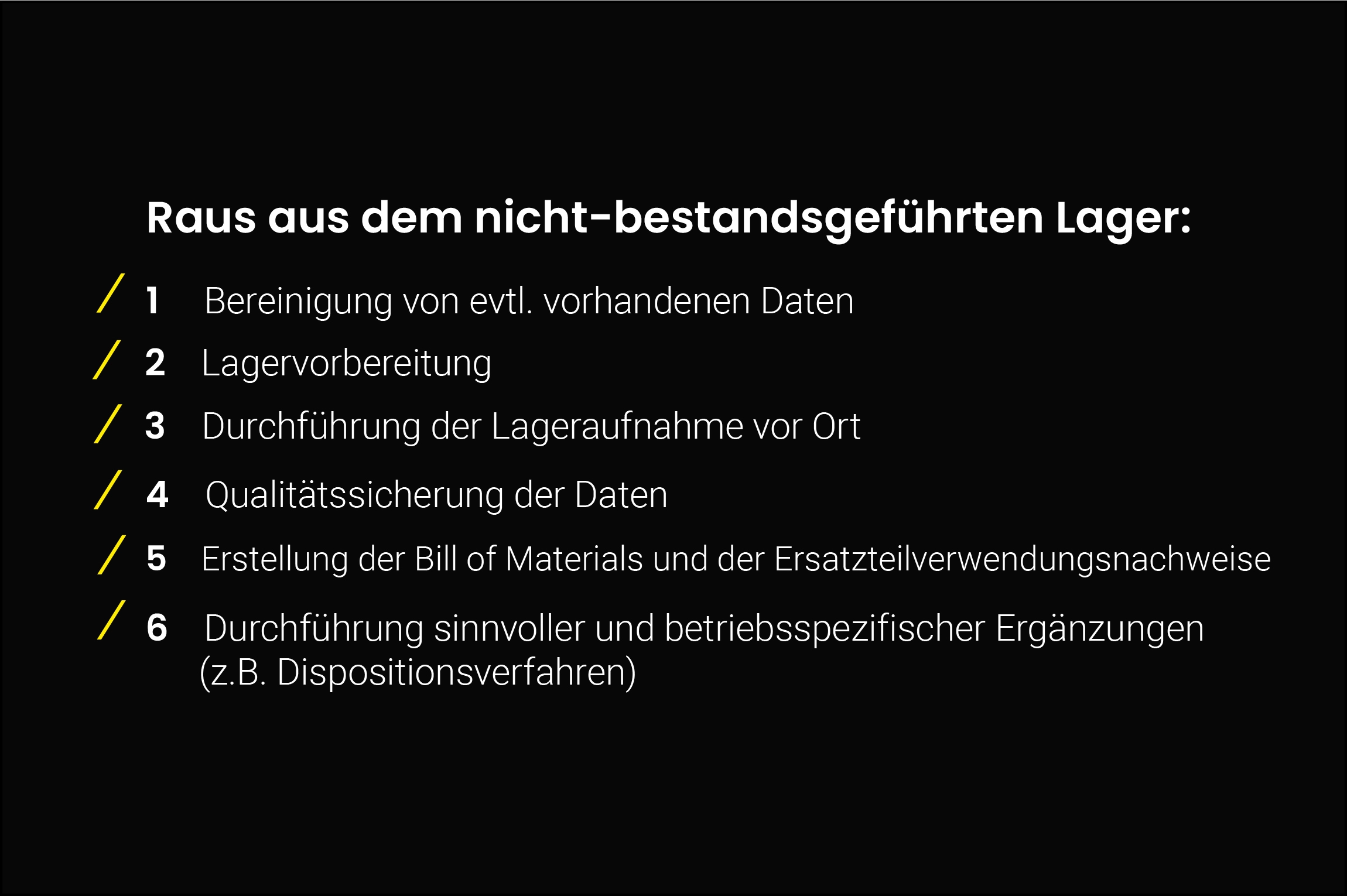
Gerne unterstützt Sie Volz-System bei der Durchführung und konkreten Umsetzung aller notwendigen Schritte, um ein optimales Ersatzteil- und Stammdatenmanagement für Ihre Maschinen und Anlagen zu entwickeln.
Nehmen Sie Kontakt mit uns auf!
5. Erstellung der Bill of Materials und der Ersatzteilverwendungsnachweise
Daraufhin können die Ersatzteilstammsätze mit den Einbauorten verknüpft werden (z.B. das Equipment oder der technische Platz). In diesem Ersatzteilverwendungsnachweis wird ausgewiesen, für welche Maschinen/Anlagen eine Ersatzteilposition bevorratet wird. Dieser Verwendungsnachweis kann dann vielseitig genutzt werden.
6. Durchführung sinnvoller und betriebsspezifischer Ergänzungen
Entweder hinsichtlich ihrer Verwendung (Einort-, Mehrort-, oder Mehrfachteil), hinsichtlich ihrer Herkunft (Originalersatzteil, handelsübliches Ersatzteil, Normteil, Nachfolgeteil, fremdgefertigtes oder eigengefertigtes Teil) oder hinsichtlich ihres Zustandes (neues Teil, gebrauchtes Teil, instandgesetztes Teil, Halbfertigteil, Teil mit eingeschränkter Lagerfähigkeit)
Häufige Fragen zum Stammdatenmanagement
Für die weltweite Konsolidierung empfiehlt Volz-System folgende Schritte:
- Start eines Pilotprojektes in Deutschland
- Konsolidierung der Werke in Deutschland
- Konsolidierung der Werke weltweit über eine mehrsprachige Klassifizierung
- Einsatz eines zumindest temporären „Vor-IT-Systems“
(Gründe hierfür sind Abschmelzungsprozesse und finanztechnische Vereinfachungen) - Wenn Sie für eine Datenaufbereitung rund 100 Arbeitsstunden ohne Datenmanager (Software) benötigt haben, so brauchen Sie mit einem Datenmanager in der Regel 25 – 30 Arbeitsstunden.
- In der Pilotphase kann überprüft werden, ob die weitere Lageraufnahme durch eigenes Personal durchgeführt werden kann oder nicht.
Wann lohnt sich eine Lageraufnahme?
Wenn man die Produktionsausfallkosten durch fehlende Ersatzteile protokolliert und mit den Arbeitsstunden, welche durch die Suche nach den Ersatzteile angefallen ist, sowie den Wartezeiten in der Produktion addiert, kann abgeschätzt werden, ob sich die Aufnahme lohnt.
Warum wir zur Aufnahme ein temporäres IT-Tool empfehlen:
Der Vorteil eines temporären IT- Vortools (Datenmanager) besteht unter anderem darin, dass die Möglichkeit einer (Mehrfach-)Klassifikation besteht. Nach der Dublettenprüfung können diverse Materialnummern abgeschmolzen und müssen beispielsweise nicht in ein SAP überführt werden, um im Nachgang die Materialnummern aus SAP zu löschen, die durch eine Dublettenprüfung anfallen würden. Auch bei einer optionalen Standardisierung der Materialien ist dieses Aufnahmetool sehr hilfreich. Die Attribute (Merkmale) können auf Baugleichheit oder Funktionsgleichheit geprüft werden. Eventuell fehlende Merkmale können firmenspezifisch und auch über mehrere Standorte ergänzt werden.